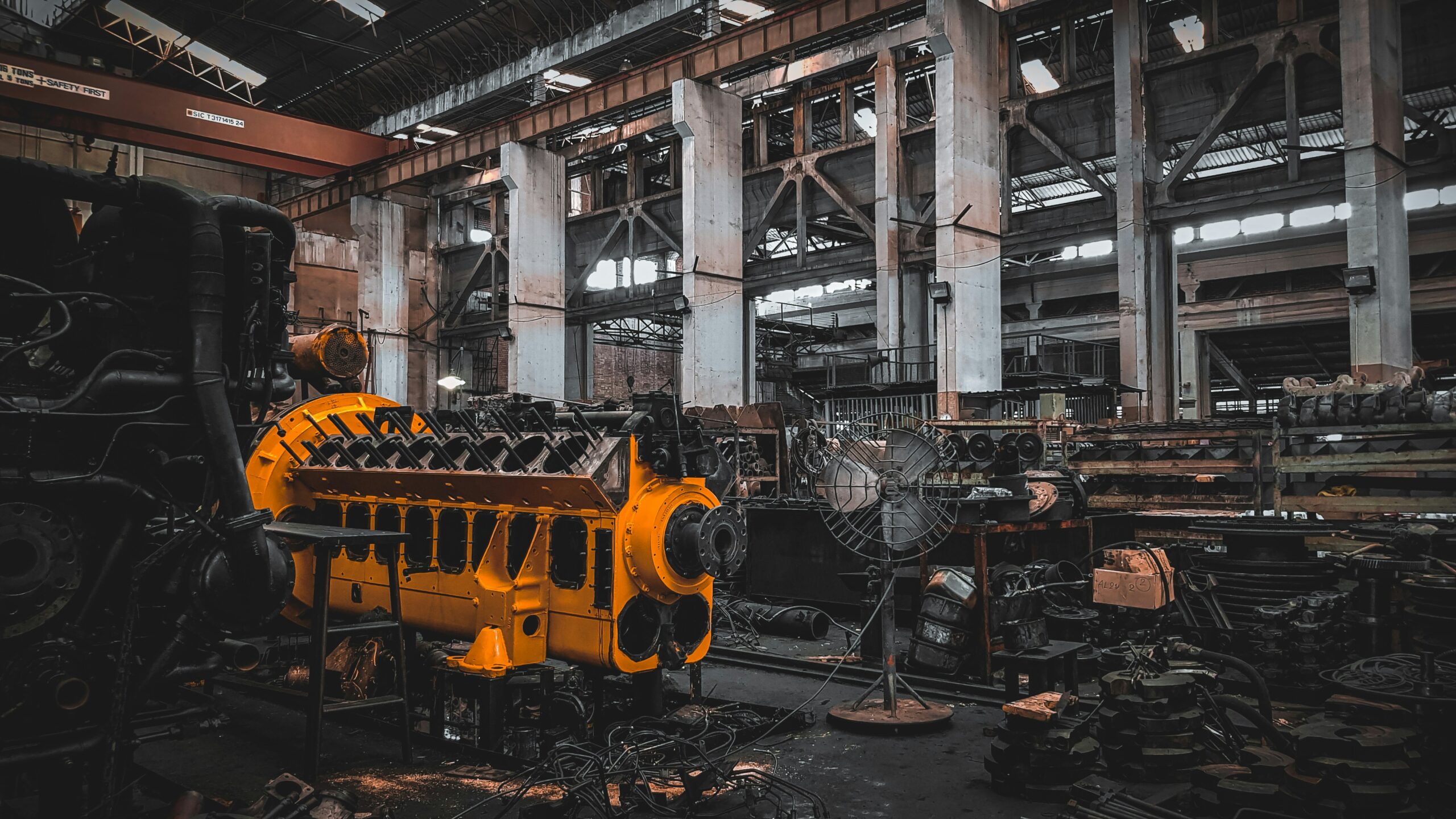
Industrial maintenance is integral to manufacturing operations, ensuring that machinery and equipment run at their full potential. It involves many tasks, from routine inspections to emergency repairs, and is pivotal in maintaining smooth operations, increasing production efficiency, and minimizing downtime. Effective maintenance practices are essential to keeping manufacturing plants competitive and productive, with industrial systems becoming more complex and integrated. In this article, we’ll explore the core elements of industrial maintenance, its different types, and the best strategies for implementation to optimize business performance.
What is Industrial Maintenance?
Industrial maintenance encompasses all activities performed to keep equipment and machinery in good working order, including repairs, inspections, upgrades, and replacements. The goal of industrial maintenance is to prevent equipment failure, reduce downtime, extend the lifespan of machinery, and improve the overall efficiency of manufacturing operations. Without maintenance, machines would experience frequent breakdowns, leading to delays, higher repair costs, and decreased productivity.
Effective industrial maintenance ensures that machines operate efficiently, reducing waste and preventing unplanned interruptions. It also plays a vital role in maintaining compliance with safety regulations, as poorly maintained equipment can pose safety risks to workers. Therefore, industrial maintenance is about keeping machines running and fostering a safe, productive, and compliant work environment.
Types of Industrial Maintenance
Companies typically employ three primary types of industrial maintenance to ensure the proper functioning of their equipment: preventive maintenance, predictive maintenance, and corrective maintenance. Each method plays a different role in keeping the equipment running and minimizing downtime.
Preventive maintenance is a proactive approach involving regular checks and servicing at scheduled intervals to prevent failures before they happen. This includes cleaning, lubricating, calibrating, and replacing worn-out parts. By performing preventive maintenance, companies can identify potential issues early and prevent costly breakdowns that could disrupt production.
Predictive maintenance goes a step further by leveraging technology, such as sensors, to monitor the health of equipment in real time. This method uses data analytics and machine learning algorithms to predict when equipment will likely fail based on patterns and conditions. Predictive maintenance helps reduce unnecessary interventions and ensures maintenance is performed precisely when needed, improving operational efficiency and lowering maintenance costs.
Corrective or reactive maintenance is performed after a machine has broken down or malfunctioned. Although this method is necessary for addressing unforeseen issues, it is the least desirable. Relying on corrective maintenance too heavily can lead to more extended downtime, higher repair costs, and reduced productivity. Therefore, it is generally used with preventive and predictive approaches to address unavoidable breakdowns.
The Importance of Industrial Maintenance
The significance of industrial maintenance cannot be overstated. Proper maintenance ensures manufacturing operations run smoothly, minimizing production disruptions and improving equipment performance. Equipment may operate inefficiently without effective maintenance, causing delays, breakdowns, and costly repairs. Additionally, poor maintenance can lead to unsafe working conditions, increased energy consumption, and lower product quality.
Maintaining equipment in good working order is also vital for safety. Well-maintained machinery is less likely to malfunction, which reduces the risk of accidents and injuries on the shop floor. Regular maintenance ensures compliance with workplace safety standards and industry regulations, protecting workers and the company from potential legal and financial repercussions.
Another key benefit of industrial maintenance is its role in energy efficiency. Regularly maintained machines tend to use less energy and operate more efficiently. This can significantly reduce operating costs, lower the plant’s carbon footprint, and contribute to sustainability goals. For example, dirty or clogged air filters, worn-out motors, or misaligned gears can cause machines to consume more energy than necessary, and regular maintenance helps identify and address these issues.
Best Practices for Effective Industrial Maintenance
To maximize the benefits of industrial maintenance, manufacturing companies must implement best practices that focus on efficiency, reliability, and safety. A structured maintenance management system (CMS) or computerized maintenance management system (CMMS) can help manage maintenance schedules and work orders and monitor equipment conditions. These tools make it easier to track maintenance activities, plan, and ensure no maintenance tasks are overlooked.
Training maintenance personnel is another crucial best practice. Technicians should know the latest technologies, maintenance techniques, and safety protocols. Regular training ensures staff members have the skills to maintain complex machinery and troubleshoot problems effectively. It’s also essential for maintenance workers to stay up-to-date with evolving industry standards and technological advancements.
Having a well-organized inventory of spare parts and tools is also essential. Keeping the necessary components on hand allows for quick repairs and reduces downtime. Regularly reviewing spare part inventories and reordering parts before they run out ensures that maintenance teams can respond quickly to issues without delays.
Adopting a proactive approach using predictive maintenance tools can also improve maintenance effectiveness. Real-time monitoring through sensors and machine learning algorithms can provide valuable insights into equipment conditions, allowing maintenance teams to identify potential failures before they disrupt operations. By addressing problems early, companies can prevent costly downtime and extend the life of their machinery.
Challenges in Industrial Maintenance
Despite its importance, industrial maintenance comes with several challenges. One of the primary challenges is balancing maintenance costs with the need for effective maintenance. Preventive and predictive maintenance strategies often require an initial investment in tools, technologies, and training. However, these upfront costs are typically offset by the reduction in unplanned downtime and long-term savings in repair expenses.
Another challenge is dealing with aging equipment. As machinery ages, it becomes more prone to breakdowns, and maintenance needs increase. Older equipment may also be more complex to repair, requiring specialized knowledge or hard-to-find parts. Companies must weigh the cost of maintaining aging machinery versus replacing it with more modern, efficient equipment.
Workforce training and retaining skilled maintenance personnel are also challenges. The demand for skilled workers is growing, and many industries face a shortage of qualified technicians. Maintaining a skilled workforce is critical to performing effective maintenance, and companies must invest in training and workforce development to ensure they have the talent needed to manage increasingly sophisticated equipment.
The Future of Industrial Maintenance
The future of industrial maintenance is closely tied to technological advancements. The maintenance industry is becoming more predictive and efficient with the rise of automation, artificial intelligence (AI), the Internet of Things (IoT), and data analytics. AI and machine learning will continue to drive the development of predictive maintenance tools, making it possible to identify potential issues with even greater accuracy.
IoT sensors will increasingly monitor machine health and performance, providing real-time data to help maintenance teams make more informed decisions. By combining IoT, AI, and predictive maintenance strategies, companies can achieve near-zero downtime and improve overall productivity.
In conclusion, industrial maintenance is essential for ensuring the’ efficient and safe operation of manufacturing facilities. Companies can optimize their maintenance strategies and drive long-term operational success by implementing best practices, embracing new technologies, and addressing the challenges of aging equipment and workforce development.